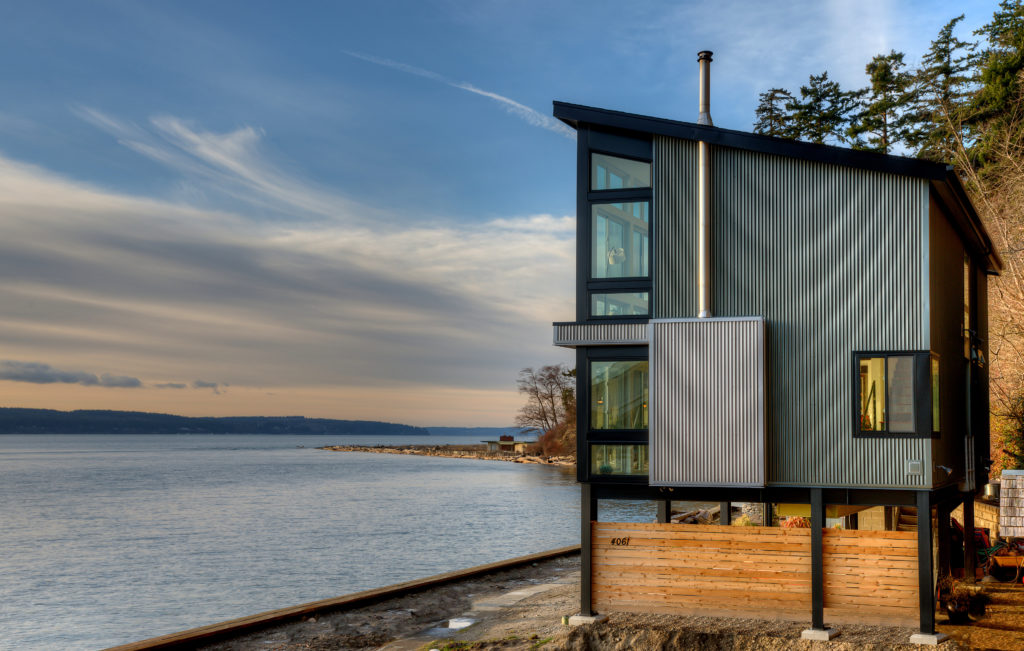
The United States gets hit by roughly the same number of hurricanes each year. But they are growing in intensity, thanks to higher level of moisture in the lower atmosphere. In 2017, two Category 4 hurricanes struck U.S. shores. The next year, Michael made landfall along the Gulf of Mexico with Category 5 force with winds of more than 160 miles per hour destroyed whole communities.
If you are planning a new home, or a remodeling project along the shore, it pays to take a close look at hurricane-resistant windows and window walls. It may even be required by code. Post-storm inspections show that fenestration can be a weak link in a home’s hurricane armor. The problem is that when wind penetrates the exterior, it creates pressure inside that can blow off the roof and crack the walls.
“Windows and doors tend to be more vulnerable to damage than other portions of a building’s envelope,” the Federal Emergency Management Agency asserts in a guide to coast coastal construction. “In coastal areas—where high winds, wind-borne debris, and wind-driven rain are common and often intense—their vulnerabilities are more pronounced.”
The easy approach to hurricane resistance would be to design a concrete bunker with as few windows and doors as possible. But a home built near the shore needs to take advantage of ocean views and breezes. A better solution is to use sturdy fenestration that’s been tested to meet hurricane codes.
Hurricane-code-approved window walls are reinforced to resist high winds. Their frames do a better job resisting water that often strikes a home sideways during an intense storm. And they are typically built with tempered glass that repels flying objects.
Many window and door companies test their products to meet tough building codes in Florida, and even more stringent ones in Miami and Broward Counties. You can typically find the tests they passed on company websites, and on the products themselves.
Other states along the Atlantic and Gulf coasts reference wind standards published by the International Residential Code (IRC) standards. The IRC publishes a wind zone map (with areas from A to D) that outlines requirements. Windows need to meet design pressures ranging from 30 to 80 pounds per square foot.
In Florida, hurricane-tested fenestration also comes with installation label. Inspectors use it to make sure installation was done correctly. Even if a window, door, or skylight has been properly anchored for structural integrity, it may leak if not correctly flashed and sealed in accordance with manufacturers’ instructions.
Window walls are typically tested as a unit that includes the glass, frame, attachment hardware, and the installation method. They are tested to meet the following three criteria:
Structural Strength
The structural strength of a window, its DP (design pressure) determines its ability to resist high winds. In testing laboratories, window walls are subjected to changing air pressure to determine when they break. Windows rated with a DP of 15 psf can withstand winds up to 78 miles per hour.
That’s not good enough for Florida or other areas subject to hurricanes. In Florida, you’d need an assembly with a DP of at least 35 that can withstand 145-mile-per-hour winds. In Miami and Broward counties, windows require a DP of 60 that can take winds up to 190 miles per hour. Stickers on the window frame provide the unit’s wind-pressure rating.
Water Penetration
In the laboratory, water is sprayed at the window walls at progressively higher velocities. Window walls with a DP of 50 are tested to resist water leakage at 7.5 psf. Unfortunately, that means that the window only resists water at speeds up to 55 mph, lower than what’s experienced during the most intense storms, according to the American Architectural Manufacturers Association.
The sealing of windows – gaskets and weather-stripping – are of key importance. AAMA in 2018 released an updated white paper on water damage during major storms. It found that even buildings that water got inside even buildings that fared well structurally, with impact-rated windows and walls doing their job. Water still leaked in around windows, doors, and skylights. It found that even code-compliant windows and doors can leak because tropical storms produce “extraordinary conditions [that] can exceed the product’s rating for water penetration.”
Impact Resistance
Hurricane-resistant windows walls are typically built with laminated glass, two or more panes of glass bonded together with a clear plastic-like film sandwiched in between. This inner “filling” acts to hold the glass together upon impact. If cracked or broken, the glass fragments tend to adhere to the plastic interlayer, preventing water, wind, or wind-borne debris from entering the building.
Impact from wind-born debris, FEMA has found in post-disaster investigations, is the principle mode of failure for window systems. To test windows in labs, 2×4 studs are fired at windows at 34 miles per hour — 55 mph in the case of Miami-Dade County testing. To pass the tests, studs cannot penetrate the windows. If they create openings, they can be no larger than 3 inches in diameter. And there can be no tear longer than 5 inches.